
2019/10 Upgrading our standard
Today Eurobatex elastomeric extruded foam pipes and sheets product line reaches the best standards among all his competitors, even the most blazoned.
In fact water vapour diffusion resistance factor (µ) has been upgraded, taking it from ≥ 7.000 to ≥ 10.000, indistinctly for all the pipes until 19mm thickness and for the sheets until 25 mm thickness.
With just one solution, Eurobatex standard product line offers the best quality characteristics in the market in terms of thermal conductivity (λ a 0°C = 0,033), fire performance European standards (BLs2d0 among all pipes line) and water vapour resistance (µ≥10.000). And this happens at the same cost, with the obvious advantages that a single product line simplifies inventory management and satisfies most demanding requirements.
What is really important to improve the implant efficiency, in order to guarantee it in time and saving energy?
The main purpose of flexible elastomeric foam for thermal insulation is the reduction of the flow of thermal energy between a fluid (cold or hot) contained in a pipe and the surrounding environment; therefore the most important technical parameter is without any doubt the thermal conductivity λ (considering that the lowest it is, the best is the thermal insulation of the product).
In particular, the insulation of pipes working with cold fluids and therefore typical of air conditioning and refrigeration systems, among its functions, in addition to energy saving, is to avoid the formation of condensation. In fact, the expanded elastomer protects the plants, on which, if not properly isolated, could trigger corrosion phenomena with related deterioration and implications also related to the development of bacteria, molds and fungi (harmful to the health of visitors in the areas concerned, for the underlying goods and equipment).
With the condensation process, a continuous flow of steam towards the cold pipeline can be triggered, that is towards the parts of the system that are not adequately protected/isolated. The flow of steam is continuous because the humidity once condensed (or iced) attracts other humidity to restore equilibrium.
We have seen how this flow of water vapour caused by condensation can favor various negative phenomena, we remind the main ones:
• Increase the thermal conductivity of the insulating material (the water leads about 20 times more than the air, the ice about 100 times) causing the progressive worsening of the situation and also entails a lack of energy saving
• Formation of a humid environment, ideal for accelerating the corrosion phenomena of the pipes that carry the fluid
• Weight increase of insulated pipes: this increase in weight can also determine the breaking of the brackets and of the whole anchoring system of the pipes.
There is another technical parameter which plays an important and synergic role along with thermal conductivity: the water vapour diffusion resistance factor, commonly called µ factor, is a dimensionless number that describes how many times a material or a product is able to resist at the water vapour diffusion comparing with an equivalent thickness of air.
The rise of water vapour diffusion resistance factor increase product performances, solving different issues in cooling and refrigeration applications. In a system where the fluid that flows in pipes that must be insulated is cold, is important, in order to prevent condensation, to satisfy two conditions: thermal insulation and a barrier against water vapour diffusion.
Let’s try to clarify this point with an example, with an “extreme example”: fibre insulation (rock wool and glass wool) is an excellent thermal insulation but has no effect in as a barrier to water vapour diffusion. This is why, notoriously, it can’t be applied on refrigeration plants.
To compare different solutions, it can be transformed into an independent and significant value: Sd, that is the resistance to the passage of steam. This is obtained by multiplying the parameter μ of the material with the thickness of the product expressed in meters: sd = μ · s (m). The obtained value represents the thickness of the equivalent air layer which opposes a resistance to the diffusion of water vapour equal to that of the specified product.
For example: we use a fibrous insulation with a thickness of 19 mm with a value of μ=3, covered with a PVC (vapour barrier) coating with a thickness of 0.3 mm with a value of μ=100000; one can easily calculate the equivalent layer of air that will be given by:
- Insulation contribution 3×0.019 = 0.057 m (thickness of the equivalent air layer)
- Coating contribution 100000×0.0003 = 30 m (thickness of equivalent air layer)
- Total air equivalent layer = 30,057 equivalent meters (equivalent air layer thickness)
If instead we replace the fibrous material with an elastomeric insulation (FEF) that is also 19 mm thick, but with a value of μ = 10000, we would have:
- 10000×0.019 = 190 equivalent meters (thickness of the equivalent air layer)
In conclusion, it can be said that, in the case described above, the protection (vapour barrier) of the elastomeric insulation is six times higher than the use of a fibrous insulator with a PVC sheet-like vapour barrier applied.
It can be noted that the vapour resistance factor μ (MU) of the material does not change with the thickness, the value Sd is instead a function of the thickness.
Even in the case of joint use of fibrous insulation with the addition of a vapour barrier of an aluminum sheet with an “almost infinite” permeability, we will have in any case a system that is based only on weak external protection: a small tear of such sheet in enough to allow water vapour to enter the system.
In fact, the presence of closed cells and the contemporary high µ value ensures the long duration of the elastomeric insulation over time.
Even in the case of damage/surface cuts of the elastomeric insulation, a certain resistance to the passage of water vapour is guaranteed, proportional to the residual thickness.
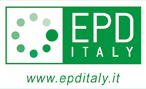
Environmental Product Declaration
EUROBATEX® HF